By Beverly Smith, PhD, Vector International
For any given business project, the successful application of Lean Six Sigma tools and techniques relies on the collective knowledge, experiences and contribution of a team of individuals. The challenge then becomes – how does one extract and harness such collective knowledge and experiences through the process of facilitation? During project execution, the project team obtains decisions and actions necessary to advance the process design or process improvement efforts. This is accomplished through effective facilitation – wherein decision outcomes must represent the perspectives of a cross-functional team or stakeholders with diverse opinions. This reality becomes a challenge for the Lean Six Sigma practitioner who has not yet mastered the soft skill of group facilitation.
Consideration for the Lean Six Sigma Practitioner:
Furthermore, irrespective of the skill level of the Lean Six Sigma practitioner, the application of Lean Six Sigma tools through group facilitation can pose unique challenges due to the nature of this type of facilitation. Some characteristics of Lean Six Sigma tools and techniques facilitation may include:
- Rigorous analysis of decision elements that make up the particular Lean Six Sigma tool or technique
- Tedious approach applied in extracting data and information from participants (The challenge here is in maintaining the participant’s level of engagement throughout the facilitated session.)
- Requiring careful attention to the operational definition of relevant terms and concepts
- The need for strict adherence to a structured or systematic approach of the Lean Six Sigma tool or technique
- Requiring solid understanding of the tool or technique being applied by the facilitator
- Direct and active involvement of process knowledge experts
Some of the common mistakes made by the Lean Six Sigma practitioner in facilitating Lean Six Sigma tool application involves:
- The selection and participation of appropriate individuals
- Inadequate preparation on the part of the facilitator and or key stakeholders
- Utilizing inappropriate rating scale for tools that involved rating such Failure mode and effects analysis – causing it difficult to arrive at a consensus
- Unclear or ill-defined purpose
- Inability to manage the cross-functional team dynamics
- Inability to arrive at a consensus effectively
- Facilitator lacks sufficient proficiency with the tools being applied
These common mistakes can be prevented with adequate preparation on the part of the facilitator. Consequently, in this article, we focus on the facilitator preparation and propose that the Lean Six Sigma practitioner treats facilitation as a standard process with specified inputs and process outputs as illustrated in Figure 1 below:

The set of process inputs (generally labeled as X) are factors that influence or affect the quality of the process outputs (generally labeled as Y) as shown in Figure 1. Therefore, the output of the facilitation process depends on the process inputs. This relationship is represented as Y=f(X).
In the Lean Six Sigma world, we generally classify the inputs to our process as the 6Ms. The 6Ms are identified as:
Manpower
Method
Measurement
Machine
Materials
Mother nature
By relating the 6Ms to the 5Ps of preparation (see Michael Wilkinson’s The Secrets of Facilitation (2004)), we identify synergies between the two approaches to facilitation preparation as shown in Table 1 below. Points of commonality between the two approaches are marked by “X” in Table 1. With the aid of Table 1, the Lean Six Sigma practitioner can interpret the 5Ps of facilitation preparation in terms of the 6Ms that drives the quality of facilitated session outcome.
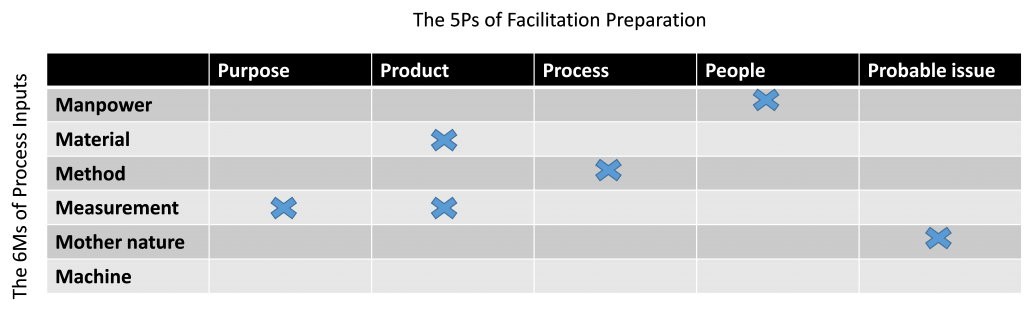
Furthermore, all aspects of the two approaches can be technology (machine) enabled or technology supported for greater efficiency. Therefore, familiarity with relevant technology is a key aspect of preparing for facilitating a Lean Six Sigma effort. For more information on the 5Ps of preparation, read Michael Wilkinson’s The Secrets of Facilitation (2004) or learn the application in the adapted training, Facilitating Masterful Meetings.
Summary
While the Lean Six Sigma training focuses largely on the “hard skills” involved in process assessment and process improvement, the application of the actual Lean Six Sigma tool and techniques requires proficiency in the “soft skill” of facilitation in order to be effective in obtaining meaningful business results.
Preparing for a facilitated session requires adequate attention to be paid to the 5Ps of preparation, which can be interpreted by the 6Ms process inputs. Adequate preparation and the development of facilitation skill will greatly enhance the effectiveness of Lean Six Sigma project execution.
This article was written by Beverly Smith, PhD, Vector International – the leading provider of Lean Six Sigma training. Learn more and get trained in Lean Six Sigma tools and techniques at Vector International.